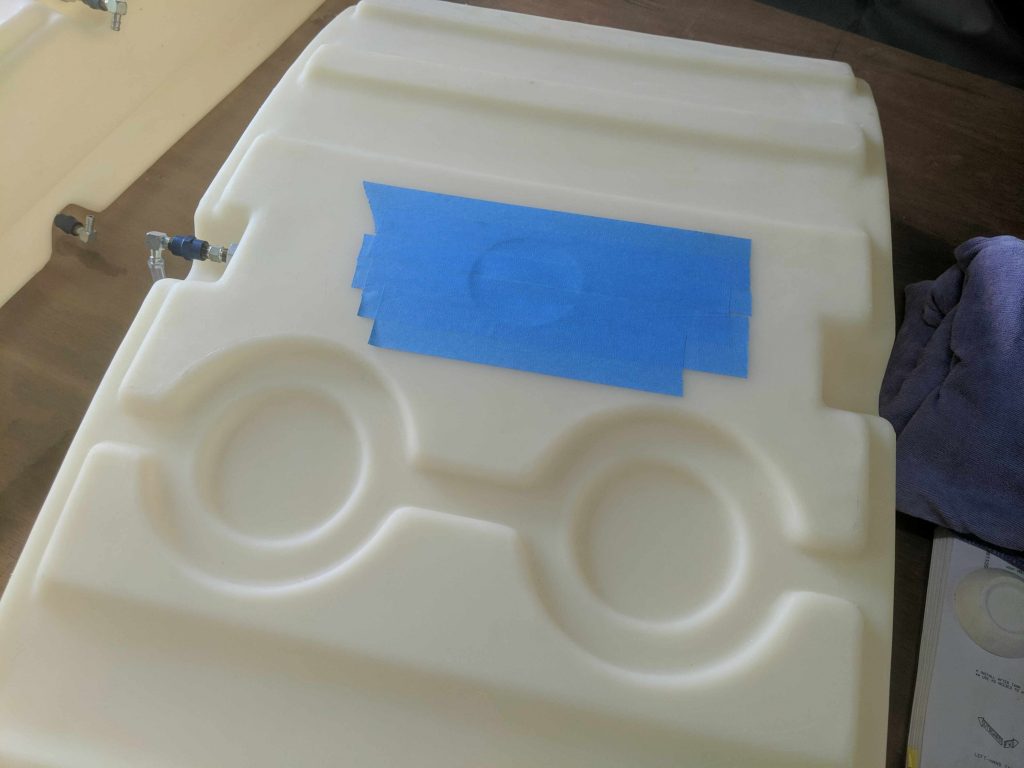
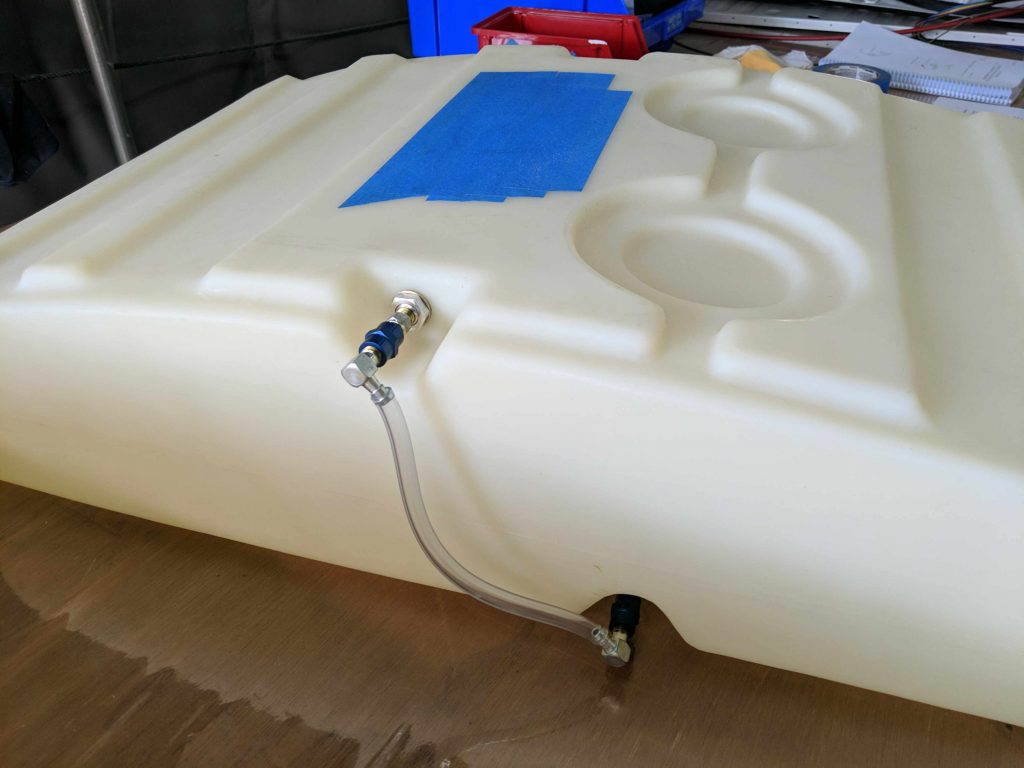
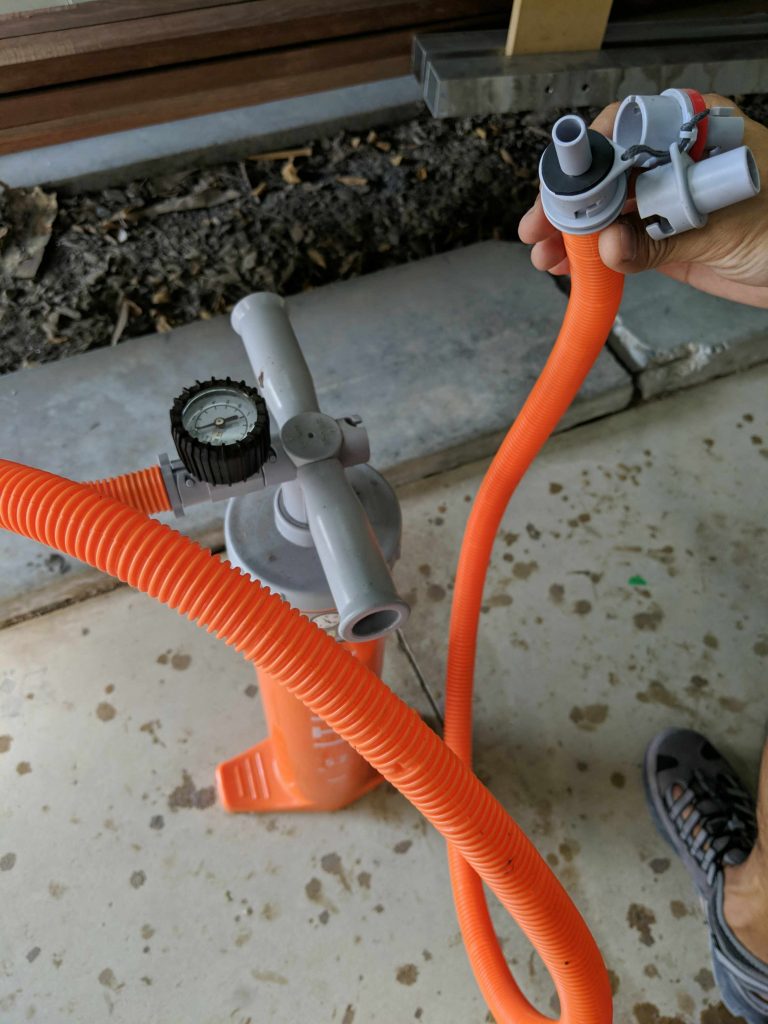
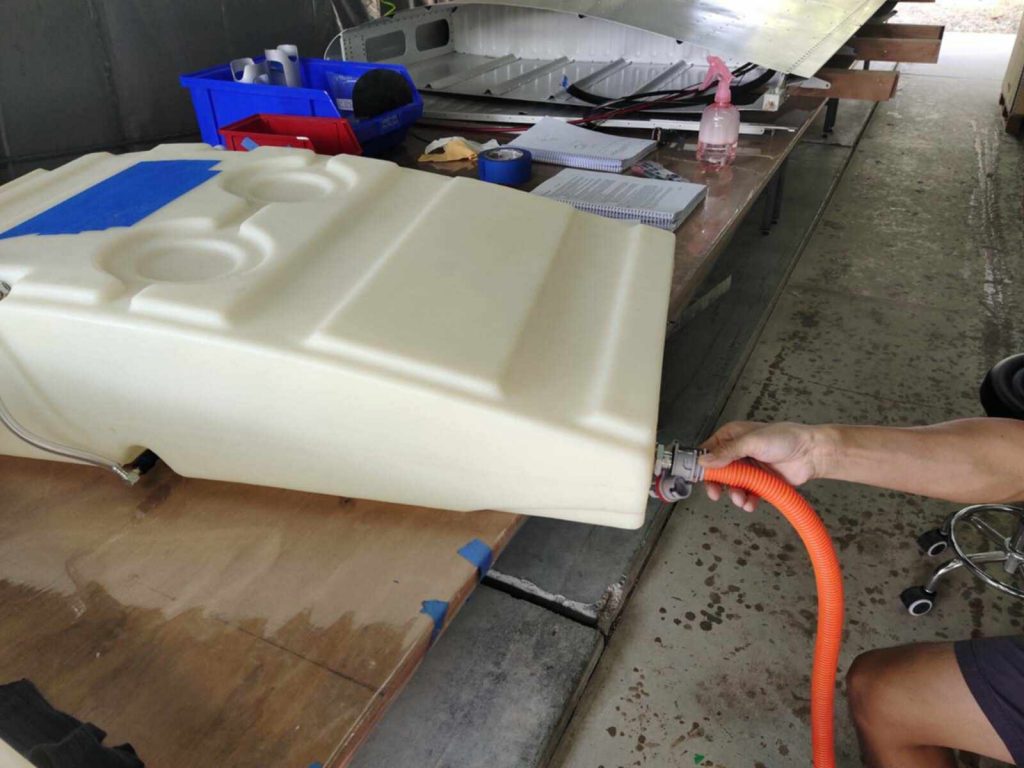
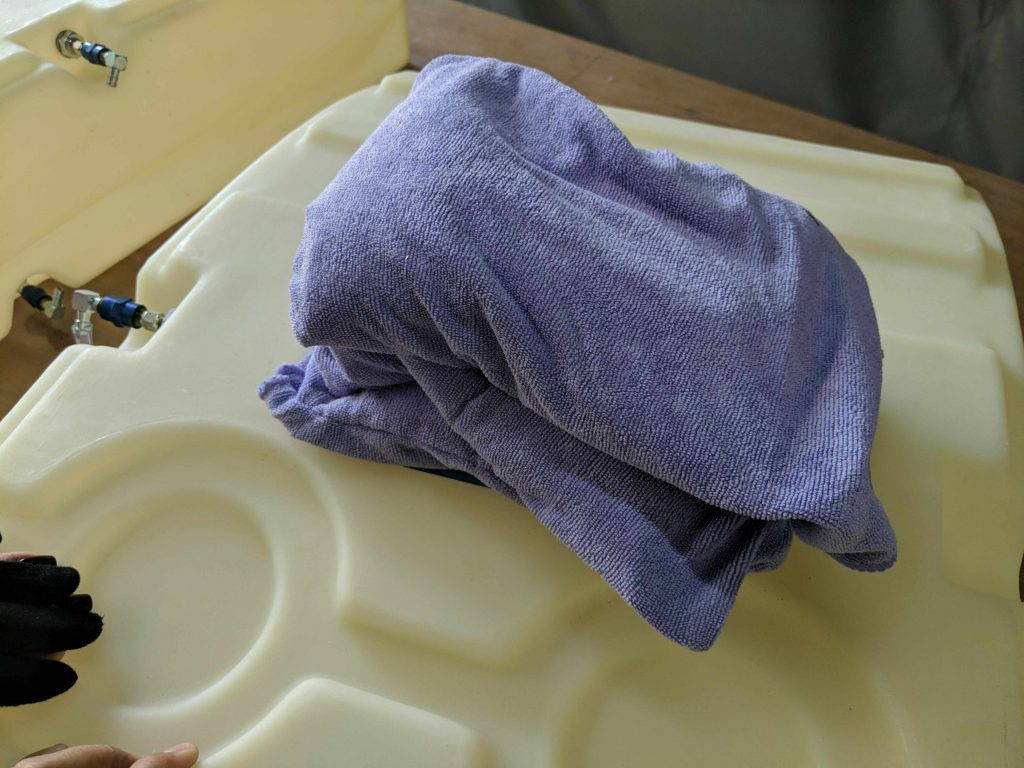
We wanted to do it quickly and be done with it quickly because we didn’t want the tanks to deform, so very few pictures from this process. (Note that a 39″ x 20″ tank has 780 roughly square inches of area top and bottom, so at 1 PSI that is 780 pounds of force on both top and bottom surfaces!)
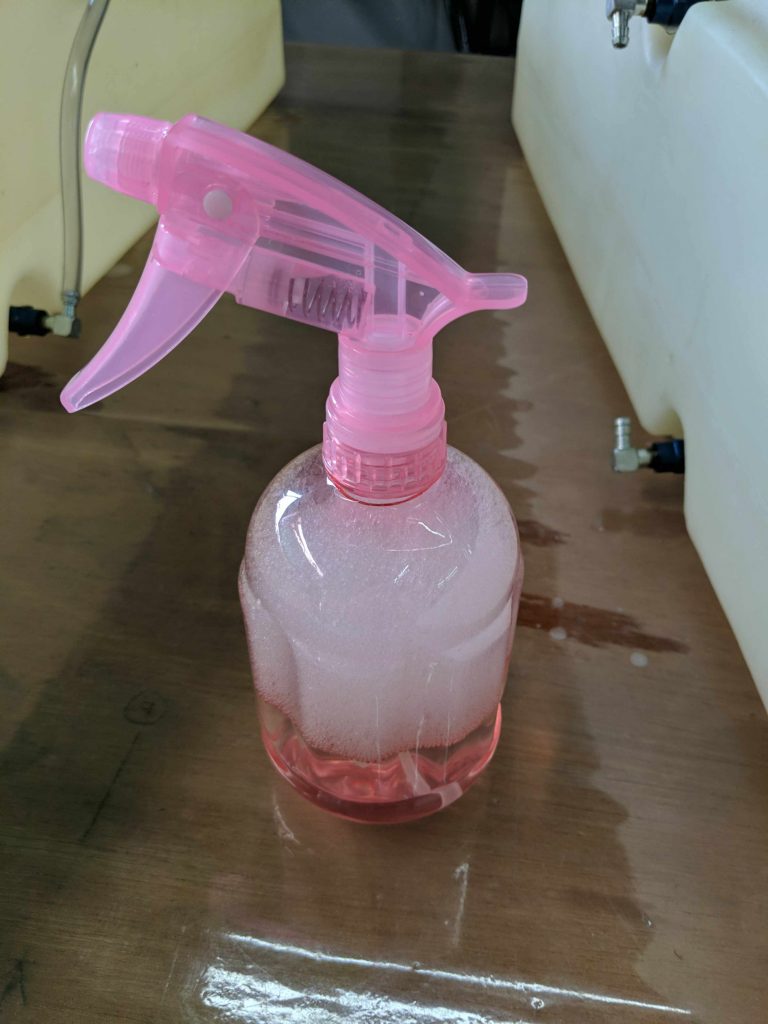
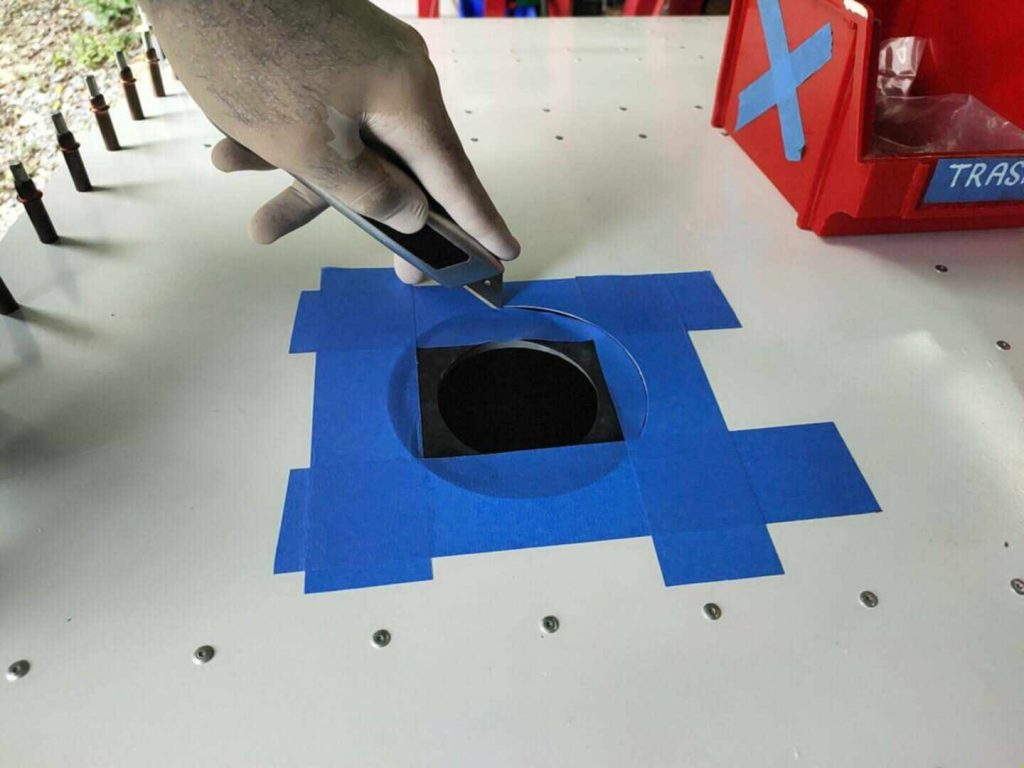
(ProSeal was very hard to source or import into Thailand, so we asked around and decided to use Permatex fuel compatible liquid gasket as that was sourceable in Thailand.)
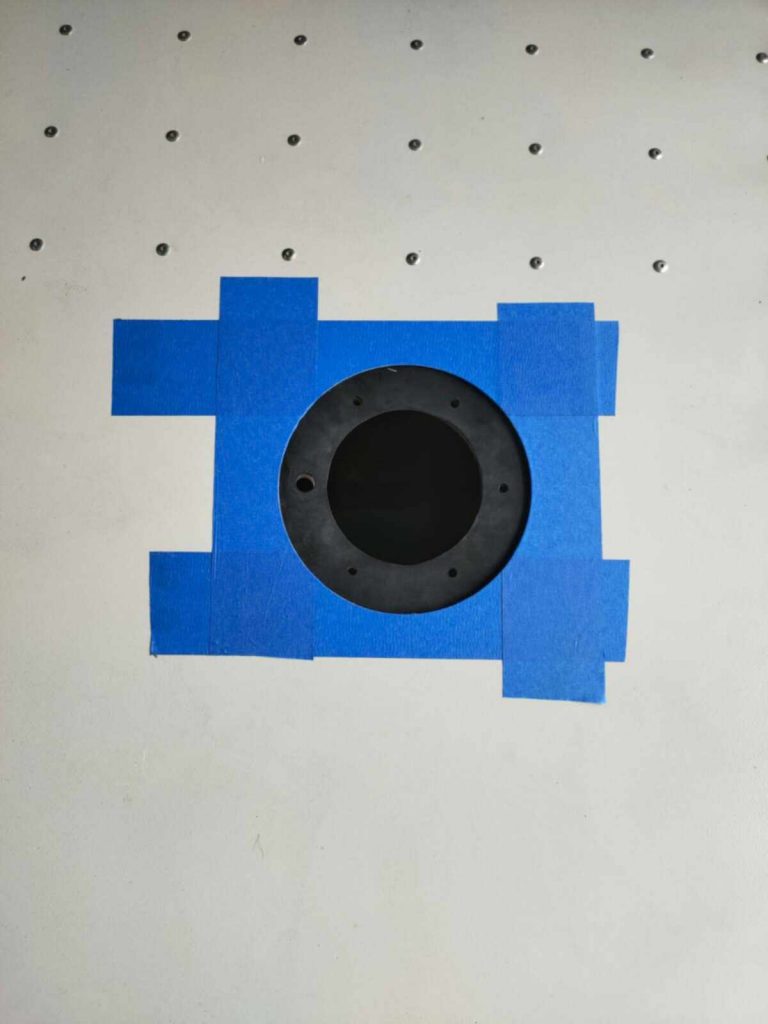
For applying the Permatex between the scupper and the fuel tank, we used two people wearing gloves to keep the stuff off our hands. (Sorry, no picture taken.) One person slides the scupper around to make different parts of the fuel tank exposed, and the other one uses a brush and tries to brush an even coat of the Permatex around the fuel cap hole and out to about 2-4cm under the wing skin.
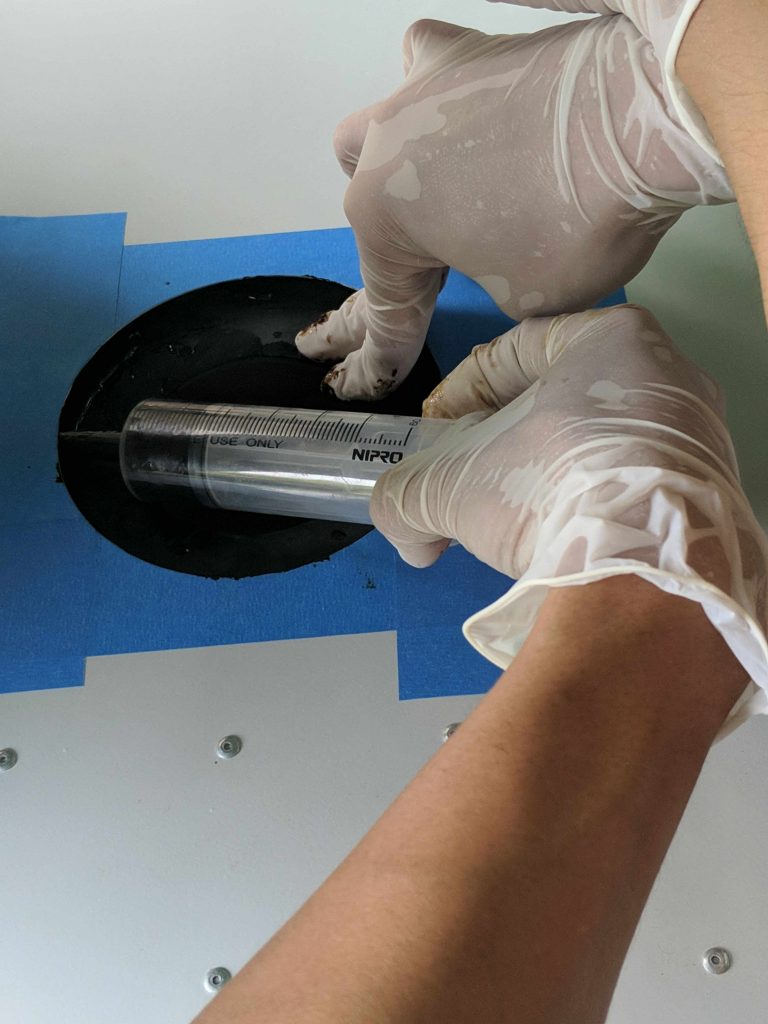
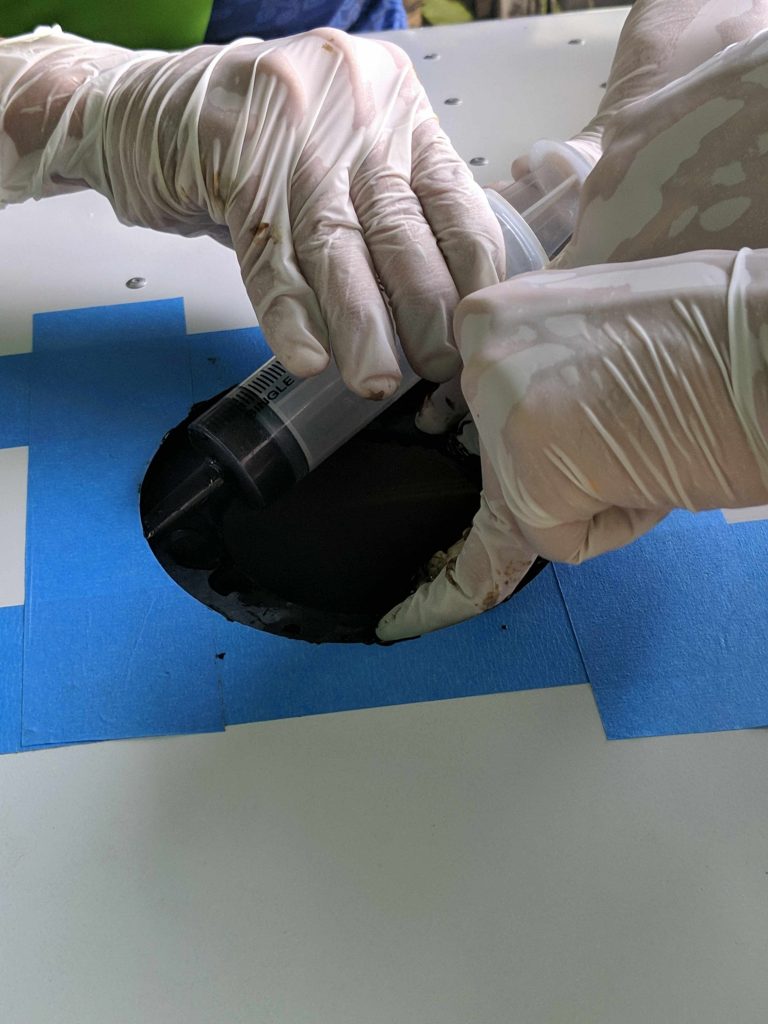
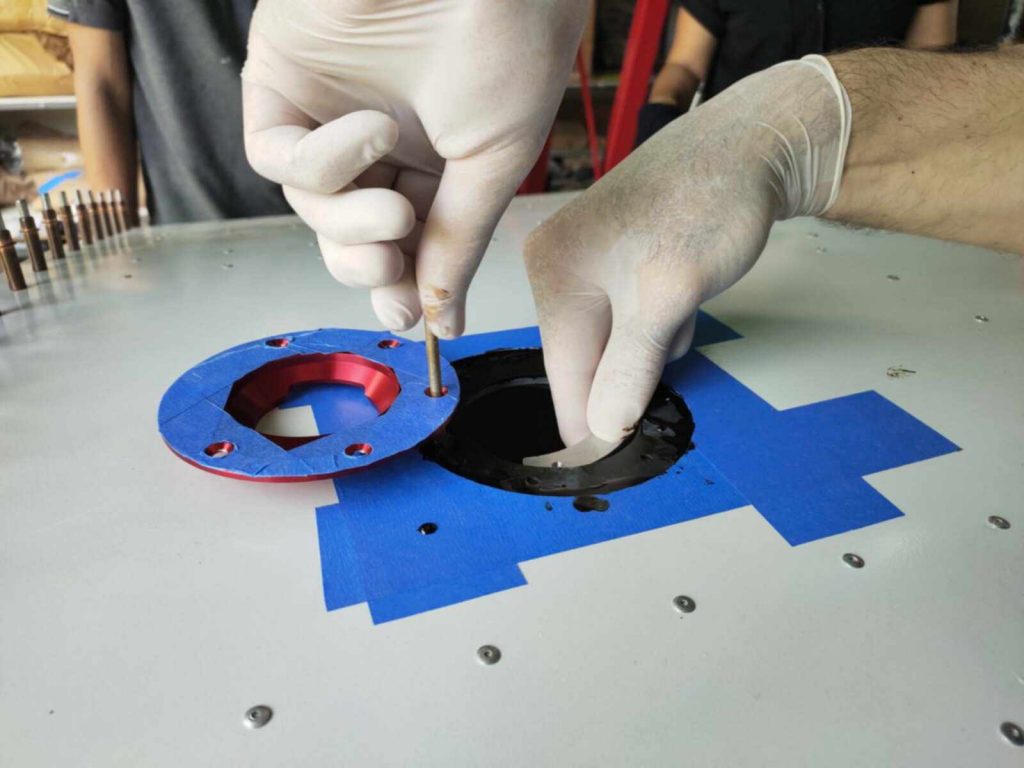
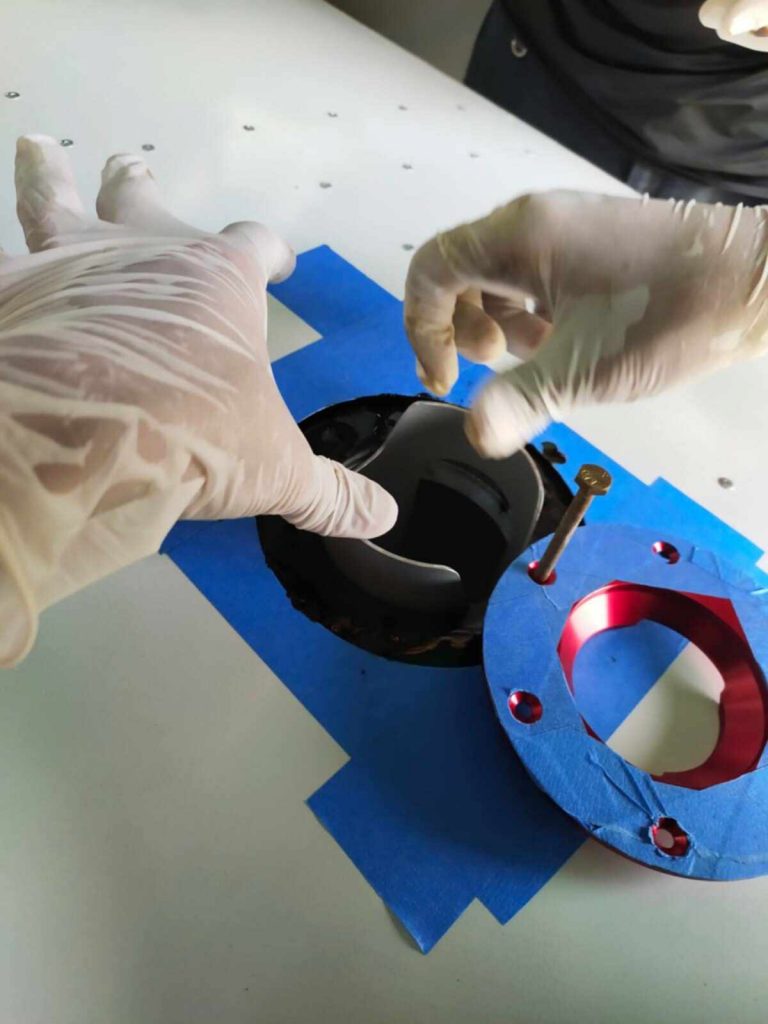
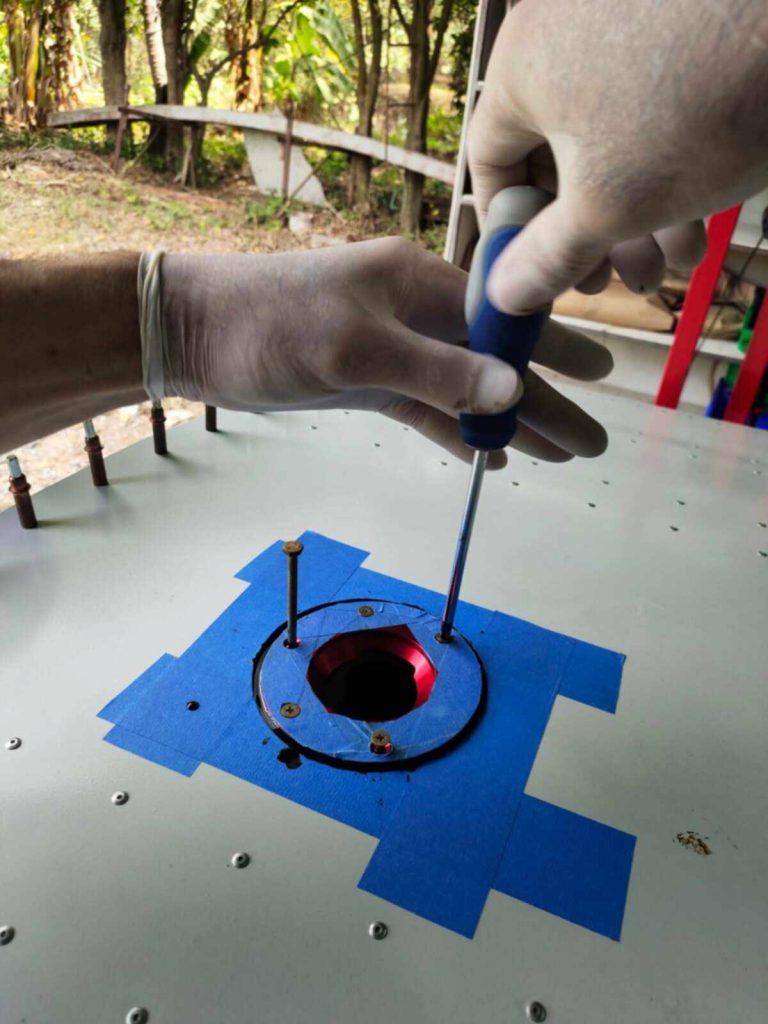
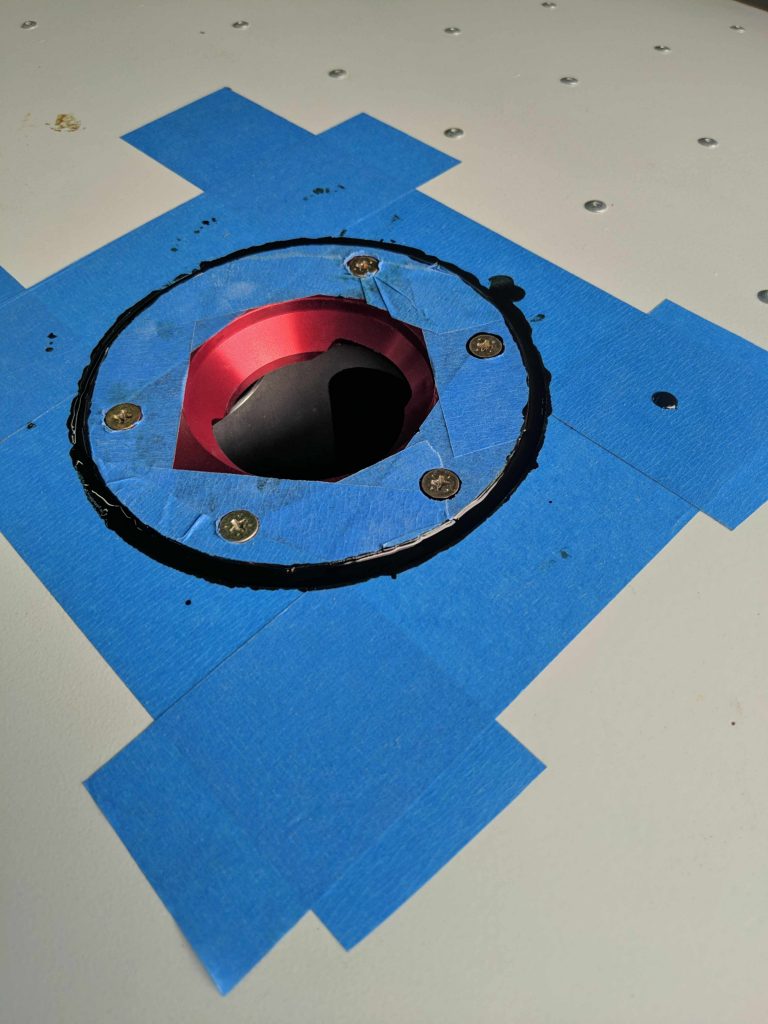
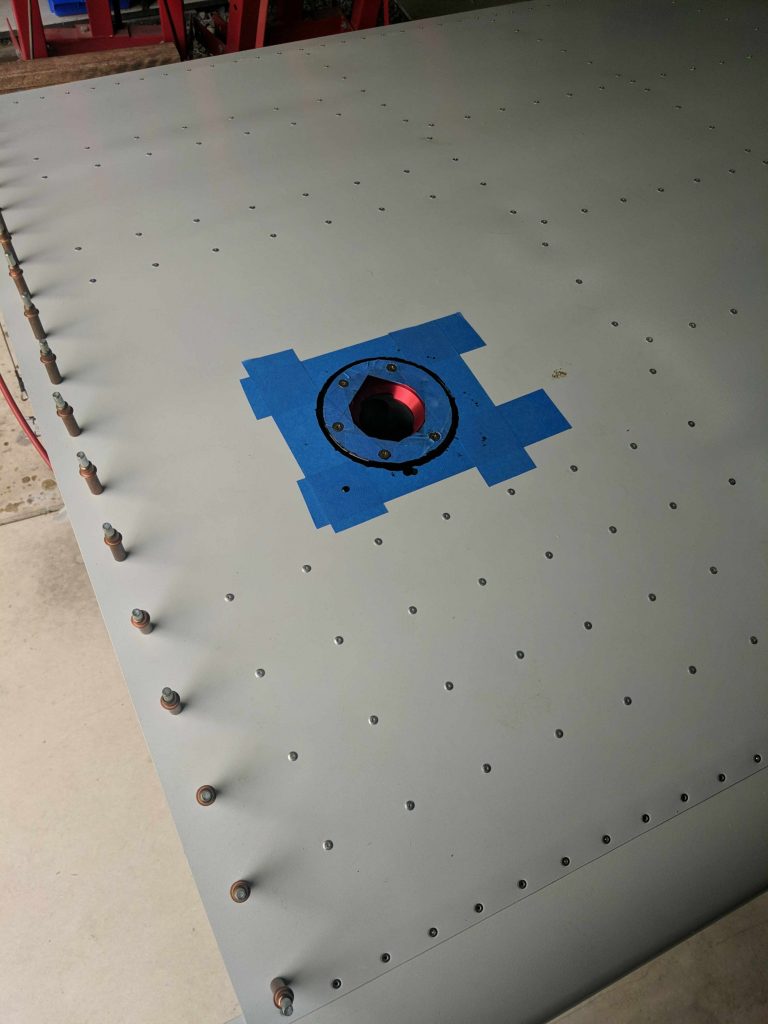